In the pulsating heart of modern manufacturing, where conveyor belts hum and robotic arms dance with precision, one innovation is quietly rewriting the rules of efficiency: Industrial Web Guide Solutions. Forget clunky spreadsheets, guesswork, and downtime—this isn’t just another tech buzzword. It’s the silent conductor orchestrating seamless production lines, and your competitors are already leveraging it. Let’s unpack why your operation needs this game-changer.
WHY TRADITIONAL METHODS ARE FAILING YOU
Picture this: A packaging line jams because a roll of material veers off-course by millimeters. Operators scramble to adjust guides manually, wasting 30 minutes—and $5,000 in lost productivity. Multiply that across shifts, and suddenly, \"minor\" inefficiencies bleed profits dry. Legacy systems rely on reactive fixes, human vigilance, and fragmented data. In an era where a 1% uptime boost can mean six-figure savings, clinging to outdated methods isn’t just risky—it’s financial suicide.
ENTER THE INDUSTRIAL WEB GUIDE SOLUTION: YOUR EYES, HANDS, AND BRAIN ON THE FLOOR

Imagine a system that:
- Detects misalignments in real-time using laser sensors
- Auto-corrects material paths via AI-driven actuators
- Predicts maintenance needs before failures occur
- Integrates with your ERP to optimize inventory
This isn’t sci-fi. Companies like FlexPack Co. slashed waste by 43% within 8 weeks of deploying these solutions. Their secret? A three-pronged approach:
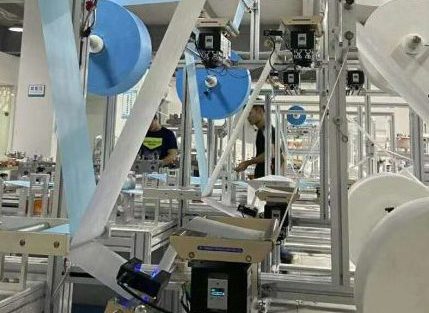
1. PRECISION ENGINEERING MEETS AI
The latest web guides use hyperspectral imaging to analyze material tension, thickness, and edge position at 200 scans/second. Machine learning algorithms then make micro-adjustments—sometimes as subtle as 0.05mm—to maintain perfect alignment. It’s like having a Swiss watchmaker inside every machine.
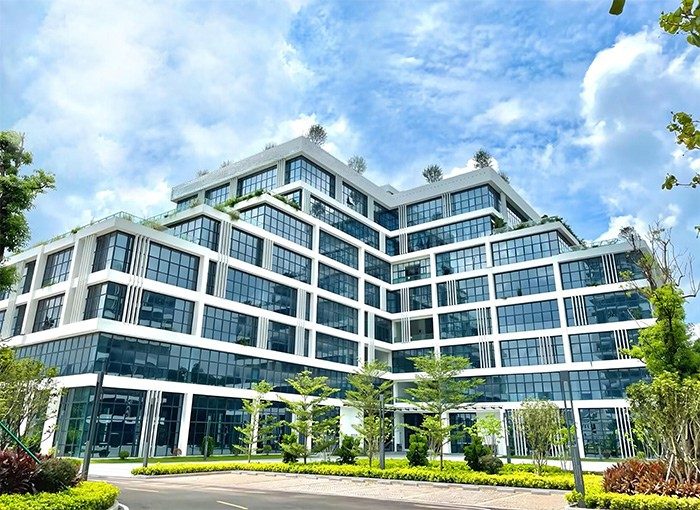
2. CLOUD-BASED ANALYTICS: FROM FIREFIGHTING TO FORESIGHT
Gone are the days of \"Why did Line 3 fail?\" Modern solutions feed data into dashboards that:
- Track OEE (Overall Equipment Effectiveness) in real-time
- Compare performance across global facilities
- Generate automated compliance reports for ISO standards
3. MODULAR DESIGN FOR FUTURE-PROOFING
Whether you’re running vintage 90s equipment or cutting-edge IoT-enabled lines, scalable web guide systems adapt. Need to switch from packaging films to composite materials next quarter? A quick sensor recalibration—not a $250k overhaul—keeps you agile.
CASE STUDY: HOW STEELTECH RECLAIMED 17,000 HOURS/YEAR
Facing chronic alignment issues in their coil coating division, SteelTech implemented a custom web guide suite. Results?
- 89% reduction in manual interventions
- 22% faster line speeds
- $2.8M annual savings from reduced scrap
“It’s like we upgraded from binoculars to an electron microscope,” says plant manager Clara Voss. “ servo press ’re seeing things we never knew were problems.”
THE HUMAN ELEMENT: EMPOWERING TEAMS, NOT REPLACING THEM
Contrary to automation myths, these systems make operators more strategic. Alerts prioritize critical issues, AR overlays guide repairs, and simulation modules train staff in risk-free virtual environments. At TexWeave Mills, operators now spend 70% less time on routine checks—redirecting energy to process innovation.
FUTURE TRENDS: WHERE WEB GUIDANCE IS HEADED
- Self-healing materials that communicate with guides
- Blockchain-tracked quality metrics for supply chains
- Quantum computing-optimized tension models
BUSTING THE 3 BIGGEST MYTHS
Myth 1: “Too expensive for SMEs”
→ With subscription models, ROI often clocks in under 6 months.
Myth 2: “Overkill for simple operations”
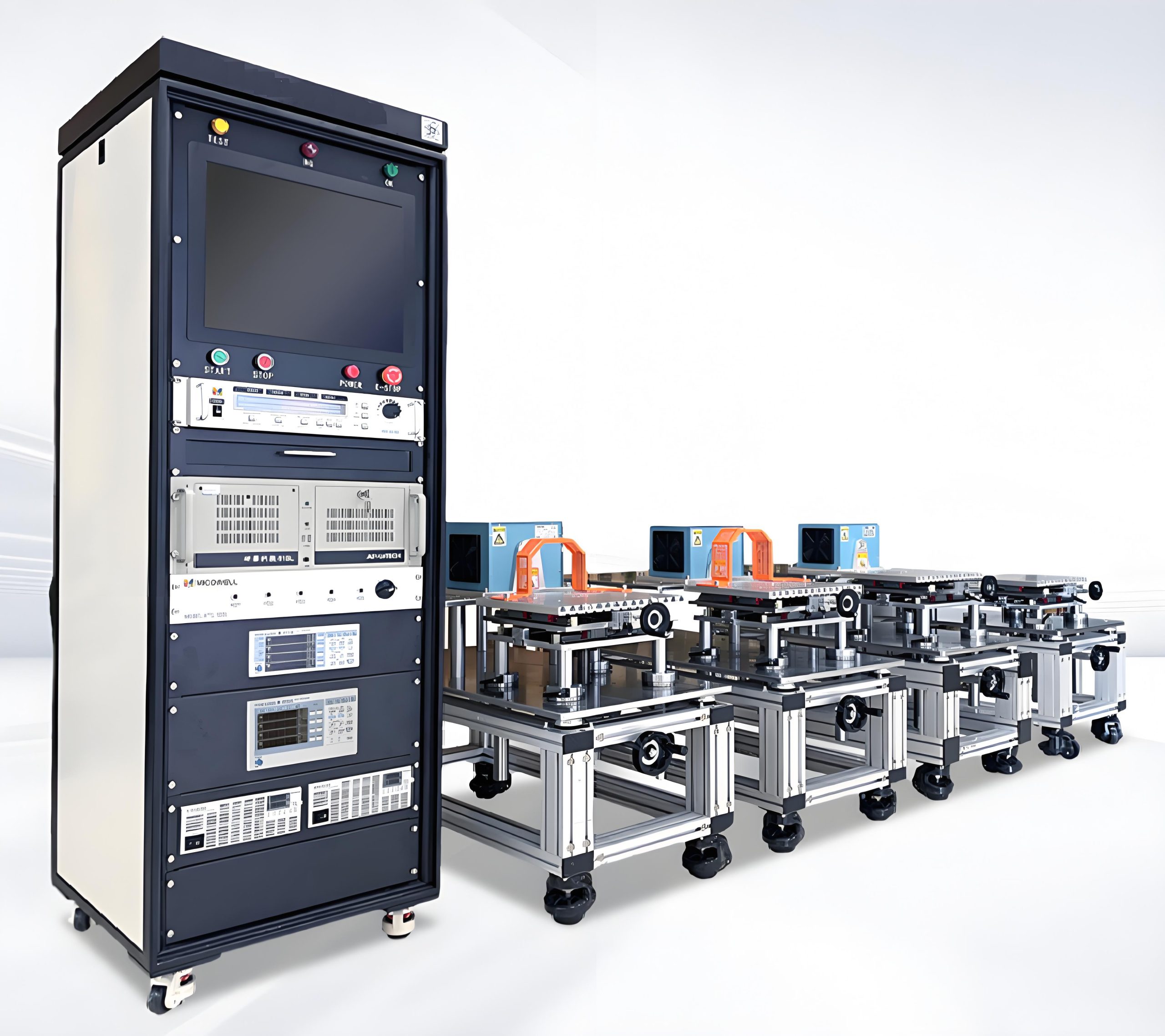
→ Even single-line setups see 15-20% efficiency jumps.
Myth 3: “Integration nightmares”
→ Plug-and-play kits now deploy in under 48 hours.
https://us.validynamics.com/?f=1&s=Automated%20CNC%20servo%20press . Audit current alignment-related losses
2. Trial a pilot project in your highest-waste area
3. Demand vendor proof—live demos, not brochures
The assembly lines of tomorrow won’t be run by those who simply keep pace, but by visionaries who let machines handle the microns while humans conquer the metrics. The question isn’t whether you can afford to adopt industrial web guidance—it’s whether you can afford not to.
Your machinery is waiting. The data is speaking. The future? It’s perfectly aligned. 🔧📈